Scuppered Scuppers
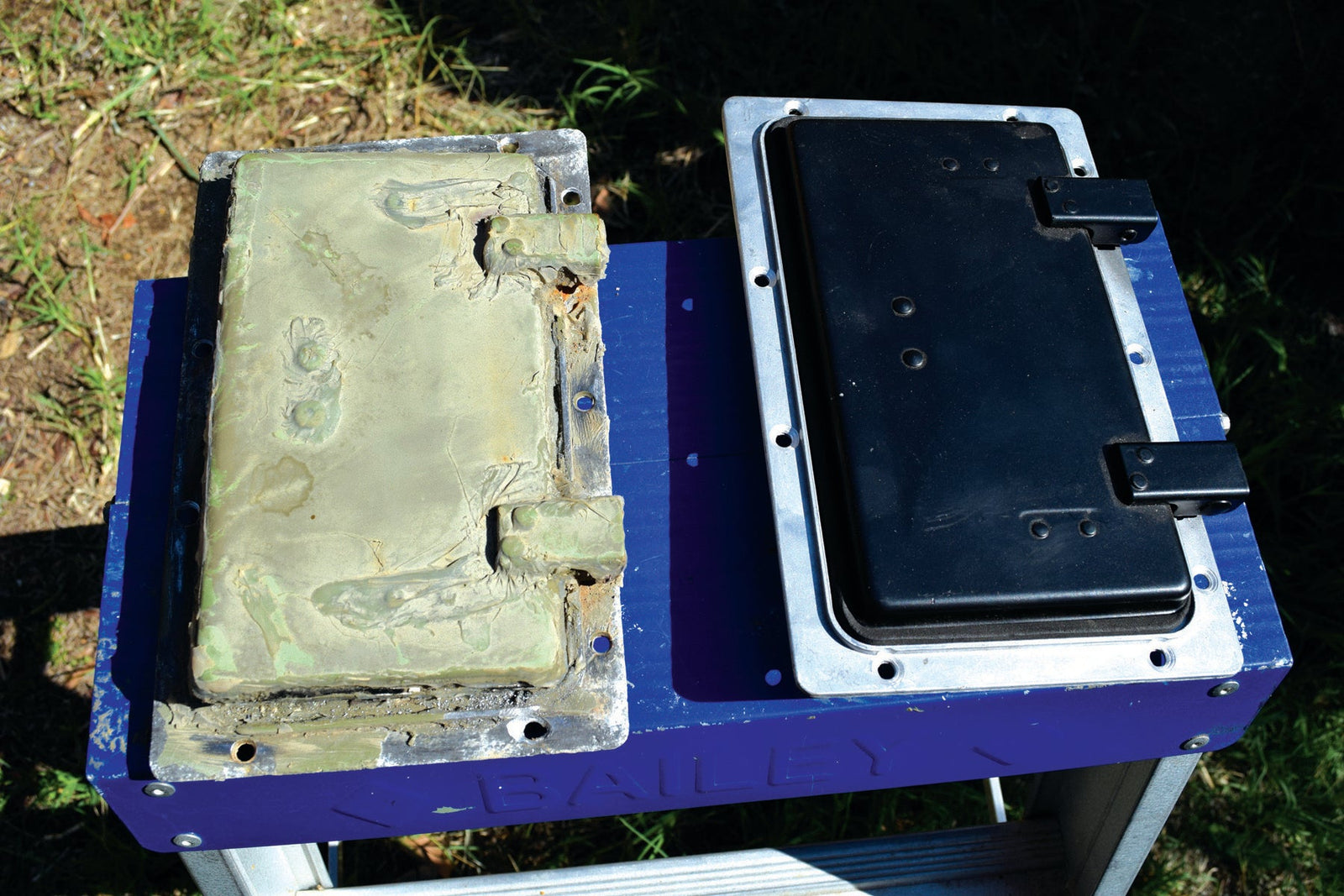
What are the two main things we try to prevent getting into our caravans and RVs? You’d probably agree the answer is dust and water. Usually caused by leaks in joins, door and window seals, vents and apparatus mounted on the roof, the campfire stories we tell about problems caused by unwanted dust and water would probably fill a book or two.
We recently acquired an ex-military 1989 6x6 Land Rover 110 Perentie along with a rear module that we’re converting into mobile home. This will be a true offroad RV, so much so we affectionately call her the B.O.V. or Bug-Out-Vehicle.
The rear module is from a General Maintenance Vehicle which had been cannibalised for parts to keep others in the aging military fleet on the road. In fixing some of the cracks in the 5mm fibreglass outer skin, I noticed the two scuppers on the roof were completely covered in silicone. You can imagine my sigh of resignation. As a 31-year-old rig, she’s verging on being an antique so it’s inevitable every problem you fix tends to reveal another. And so it was in this case.
Scupper vents are a popular method to reduce dust ingress into caravans and other RVs. They’re designed to scoop in air under pressure as you travel forward. This raises the interior pressure to a state of positive pressure, preventing dust from entering the rig from small gaps when travelling on dirt roads. Of course, this only works provided there are no flaws in other seals and joins, and you haven’t left a window open!
In this case, it was clear the scuppers were not as they should be, and chances were, hidden problems were waiting to be discovered alongside those I could plainly see. It was time to investigate.
Sure enough, once I started to peel back the inordinate amount of clear silicone around the vents, it became evident that every screw-head for both scuppers was burred over. Also, one scupper had a busted spring mechanism. This was going to be a bigger job than I’d originally anticipated.
STEP 1: BURRED SCREWS
To solve the problem of the burred screws, I opted for the Easy-Out Extractor Screw Set. To utilise this device, first drill a pilot hole in the exact centre of the screw. Accuracy is important here or else you’ll snap the extractor in the next stage. As Murphy’s luck would have it, the supplied drill bit snapped on the first screw. I replaced it with a Cobalt Drill Bit and had a lot more luck. Cobalt drill-bits have 5–8 per cent of cobalt in the steel alloy which increases their strength, making them well suited to drilling into hard metals.
For nine screws, the Extractor Set and Cobalt drill-bits worked well. But on the other nine, the extractors kept breaking. I put this down to two factors. Firstly, some of my pilot holes simply weren’t dead centre. But the other problem was that in places the scupper was affixed using countersunk Philips head bolts, not screws. When removed, these bolts revealed extensive rust on their ends. It was also plain to see that, on original installation, the bolts were placed in with some kind of thread locker that didn’t want to let go.
STEP 2: BURRED SCREWS (CONT.)
Faced with a set of uncooperative bolts, I decided to bore out the bolt heads (including their embedded snapped extractors) and then lift the scupper off. I then used a pair of pliers to unscrew the bolts.
In doing this, some of the nut rivets from the bolts came loose in the aging fibreglass. Nut rivets, sometimes called nutserts, are rivets that have a thread inside them. This means that, once you complete the rivet, you can place a bolt into them. This is a handy feature for fitting anything on your caravan or tow-tug that you think might break and need replacing in the future (basically anything with moving parts or does not have access to the reverse side). In my case, the consequence of the loose nut rivets was that they spun in place, so I needed to apply pressure onto the nutsert to hold it down while burring out the bolt heads.
After removing the scupper it was clear why 15 kilos of clear silicone was added around the vents. On original installation, the manufacturer had used a low-grade household silicone, and not much of it. This had dried and crumbled allowing water ingress. The silicone fix-it job that had first caught my eye was obviously an attempt by a military mechanic to get the rig quickly back on the road during its operational service. I’ll forgive him for that.
STEP 3: REMOVE RIVET NUTS
With the original rivet nuts having become loose, they needed to be removed and replaced. I chose to knock them all out with a nail punch and collect them from the cavity underneath. I then utilised a drill-bit to clean up the holes and make them one-size larger to match the make and model of nut rivets that I’d be using.
After that, I simply cleaned the surface for the next steps.
STEP 4: NEW NUT RIVETS
Next choose the size bolt and nut rivet you wish to utilise and match it with the correct threaded mandrel/bit size for your nut riveter. Place the mandrel on the tool with the handle/s in the open position. Place on the nose piece and select desired depth (this is important so that you don’t damage soft materials or strip the thread of the nut or mandrel on harder ones). Thread the new nut rivet on to the mandrel and then push the nut rivet into the pre-drilled hole. Press the handles together to compress the nut. This makes the bottom of the rivet ‘bulge’ and compress onto the parent material. Unscrew the mandrel from the nut rivet and repeat — in my case 17 more times.
I used the Kinchrome 68 Piece Twin Handle nut riveter for my job because it comes with six nut rivet size options (M3, M4, M5, M8 and M10). This gives me flexibility for when I do other jobs down the track that need larger bolts. There are smaller nut riveter kits available, so take your pick depending on your budget and particular needS.
STEP 5: WATER PROOFING
While waterproofing with a household grade sealant was the preferred option of the original manufacturer, I wasn’t about to make the same mistake. This time the new scuppers were getting a generous application of Sikaflex 227. It’s a purpose-made automotive sealant that’s fit for vibrations, can be painted over if you mess it up, and has sound deadening properties.
STEP 6: FIT NEW SCUPPERS
We found new scuppers online that matched the originals so we could use the same drill holes. This is where you’ll find out whether you messed up your hole alignments. Slowly insert the scupper into the cavity and align the holes with the nut rivets. When they line up, start screwing the bolts in, in an alternating order (bottom left then top right, etc), finger tight at first, then one last tighten when they’re all in. To ensure these scuppers are 100 per cent waterproof, we added one last bead of Sikaflex 227 around the outside.
Job done and dusted. Or, I should probably say ‘done and dust-free’.