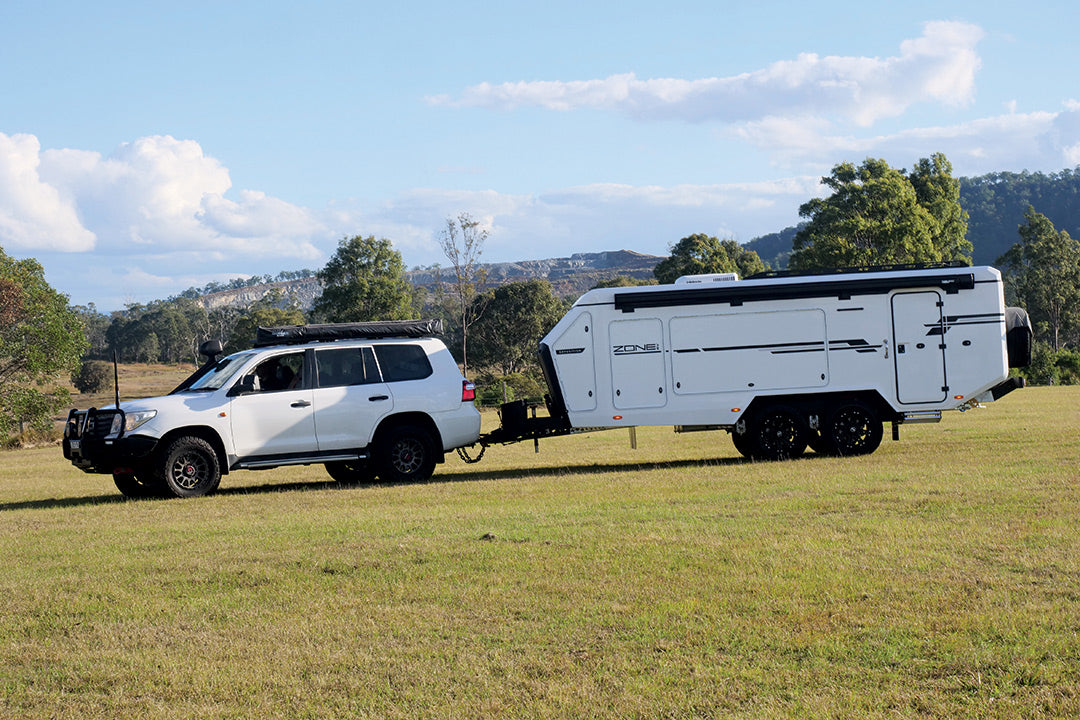
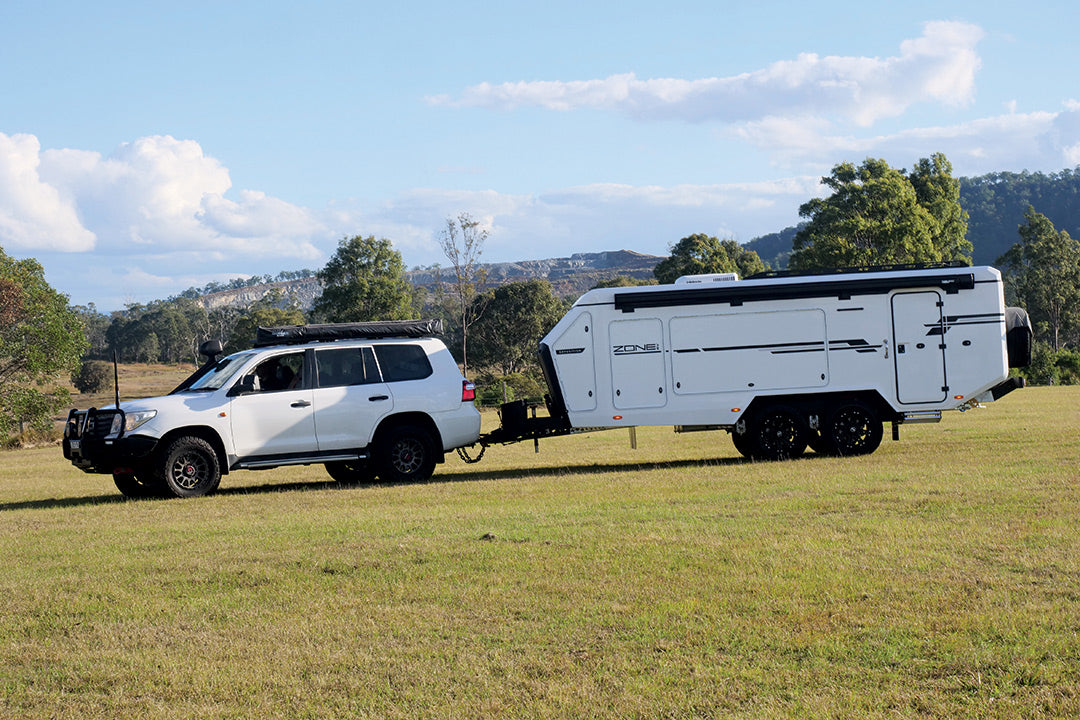
We tour Zone RV’s factory in Coolum Beach, Qld, to find what makes these vans so special. And the 3D printer is only one aspect that impressed us.
When Zone RV started up in 2016, company founder Dave Biggar told the world he intended to build the most innovative new offroader. At the time, even for a Queenslander, that was a big boast. But within a year or so, Zone RV won the prestigious Caravan World Best Aussie Van event with its Z-20.6 by wowing the judges with the great build quality, composite materials and structure and innovative approach, so the brand was on the right track.
And now, Zone RV has earned a wide following, and its range of offroad, self-sufficient caravans is considered among the best available.
Much of the brand’s success is due to Biggar’s experience building lightweight, high-performance composite sailing boats and composite panels for the wider automotive industry. Alongside Zone RV, Biggar also oversees Cure Marine, ONE Composites and Mode 4x4 Canopy, so there is much cross-pollination of ideas and improved processes.
Zone Expedition roof sections at ONE Composites
Zone RV's impressive new 3D printer
Zone RV recently added the innovative Expedition pop-top to its lineup of two full-height caravans, each with two equipment levels. While the term innovation sometimes stretches to the mundane in some caravan promotions, Zone RV has taken innovation to new levels with the introduction of a monster 3D printer.
According to a Queensland government announcement, Zone RV acquired the printer thanks to a $1.16 million Made in Queensland (MiQ) grant that allowed expanded production and created nearly 100 new jobs. Around the same time, the company invested in a $7.5m, 5000 square metre facility in Coolum Eco Industrial Park on the Sunshine Coast.
The printer is the largest in the southern hemisphere and is housed in a dedicated room in one of Zone RV’s factories. The Virtual Smart Factory VSF122 is a gantry-based computer-controlled robot that prints and machines over a 22m x 5m x 1.6m footprint.
The new 3D printer at work
The 3D printer does not produce the actual caravan panels or parts. Instead, it forms a plug, which is the exact shape of the desired component, and a mould is built from the plug. Workers then make the parts by laying a top layer of gelcoat into the mould before introducing sheets of fibreglass matting and carefully cut foam insulation. They then cover the mould with a silicone bag and introduce carefully measured vacuum-infused resin. The result is a perfectly formed fibreglass component that can be as big as the caravan roof or walls and as small as a furniture bracket. There are 25 fibreglass parts in an Expedition pop-top originating from the 3D printer, including the two 5.5m side sections.
Using the new printing technology, Zone can introduce new designs quickly on its computerised 3D CAD geometry. Making the complicated mould for the Expedition’s roof by hand would take weeks of meticulous modelling, whereas the computerised process can fashion the plug overnight.
A robot trims the wall mouldingThe vacuum moulding line
Composite build construction designed to last
All Zone RV caravans derive their immense strength from the composite build process. Like a sailing boat, the joined panels are permanently bonded together, and each component interlocks with its neighbour to form a permanent monocoque construction. Complicated shapes in the Expedition also add to strength. Scalloped edges and curves are much stronger than a flat section, in the way corrugated roofing iron is much stronger than its flat steel equivalent.
With loads of room across three modern factories, the workspaces are open and clutter-free, with ample light and ventilation. As we toured the factories, the workflow seemed methodical and steady. Most stations had three vans in various stages of construction, with an average output of two completed vans rolling out the door each day. The current staff is around 250 employees across the design, production, administration and a sales team in the indoor showroom.
Fitting the interior of an Expedition model
Following the assembly process of Zone RV's vans
Zone RV’s lineup comprises three basic models: two full-height caravans, the Sojourn and the Peregrine, and the Expedition pop-top, which we will follow through the assembly.
Each build starts with the purpose-build chassis fabricated from Australian steel in a dedicated factory. It is then hot-dip galvanised and heads to the production line, where it’s loaded onto a chest-high dolly that’s wheeled along as it progresses through the factory.
The Cruisemaster independent suspension, fibreglass water storage tanks, air compressor pump and tank and composite battery box all go onto the bare chassis, and the team starts running wires and water leads while there is easy access. Metal stone shields go over the tanks, and there’s provision to lower the fully sealed battery box if needed down the track.
The vans are now ready for the one-piece composite floor, which is predrilled on robotic machinery for the exact location of openings and slots for the cabinetry and then bonded to the chassis with two-pack epoxy.
Meanwhile, the furniture is assembled in a dedicated workshop. A CNC machine cuts composite panels to shape, which are then fixed together with interlocking mortice and tenon joins and glued with a rapid-set German two-pack adhesive into a secure and robust structure before they are sent to the production line.
Fibreglass being cut on the CNC machine
Zone RV builds the vans from the inside out, so the furniture is the first component to be set in place and bonded to the floor in its precise location. Any floor openings are sealed so there are no penetrations, leaving the cabin airtight and dustproof. The furniture combines composite panels and lightweight aluminium strengthening supports, making it timber-free and rot-proof.
The wall sections are located, and we are told the positioning has a .05 per cent tolerance. Each side wall panel wraps around to also include half of the front and rear walls, so there are only two joins instead of the usual four in most caravans. The sections are permanently joined and covered with a fibreglass mould for extra strength and aesthetics.
The roof is fitted
Roof actuators are installed, and a gantry crane lifts the roof into place. The crew has already installed as many as six solar panels and the air conditioner to speed the process and avoid the team working at heights. The side curtains are installed, and final touches are made to the interior with upholstery and appliances.
Outside, the hatches are fitted, and I noted quality triple-sealed automotive seals and robust Italian Zadi locks for efficient dust prevention.
As the caravan moves through the line each station has a quality control (QC) assessment and rectification. The final QC process goes through a thorough checklist and a water test before handover at the Zone RV factory.
A unqiue handover process
Keeping with Zone RV’s commitment to customer satisfaction, the brand now has a handover team at Hangar O, north of Gympie, Qld. This bush camp is set up so that new owners can take their time familiarising themselves with their caravan under the instruction of property owners Darren and Dee before heading off on their first adventure.
We had the chance to review Zone RV's new Expedition pop-top van in issue 654 of Caravan World and online here, so check it out now.
THE NEXT STEP
If you want to learn the latest caravan news, find the most innovative new caravans, tow vehicles and camping gear or get inspired to plan your next adventure to some of Australia's ideal spots off the beaten track, subscribe to our weekly newsletter. We promise to send you only the best content.
Related articles:
Caravan review: Zone RV Sojourn
Caravan review: Zone RV Venture 22.6