Welcome to New Age
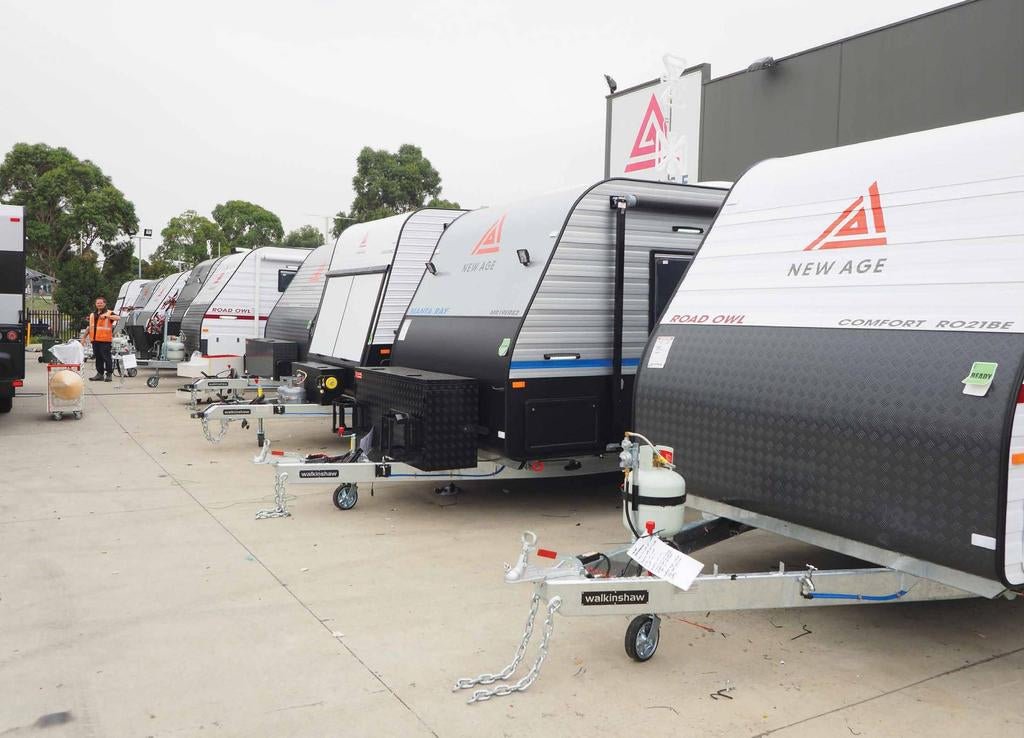
Like all fashion, time changes everything, and some of the more adventurous colour choices haven’t stood up in the more conservative 2020s. And while we have seen a trend back to timber as a feature, it's unlikely the heavy timber fitout will return.
Within a few years, production rivalled the prominent manufacturers, and by 2012, the company had moved into a $10m factory complex in Melbourne's north-west suburb Epping. When The Walkinshaw Automotive Group (WAG) was looking to diversify its operation, they saw an opportunity to enter the recreational vehicle market through a joint venture with New Age Caravans, which was converted to full ownership in 2019.
Walkinshaw’s automotive engineering background brought new methods and design skills, which soon showed in the vans. WAG applied their research, development, and testing procedures to the vans and evaluated designs with their ten-post test rig — the only one in the country — and at their test track.
WAG’s background in automotives meant they were soon very much across the Australian Design Rules and the Standards for caravan design. Improvements included a Walkinshaw-designed chassis with main rails running from the back of the van right through to the hitch. The chassis is both lighter and stronger without any welded joins in the length of the mainframe. You may notice too that the rear end of the New Age vans is similar across the range. The moulded ABS panel includes lights and a spare tyre, which simplifies production and ensures no errors in the compliance process.
When we visited the sprawling 23,000sqm New Age factory complex earlier this year, Victoria was in the early stages of COVID-19 lockdown, and work numbers had been reduced to fit government regulations. Nonetheless, production continued within the New Age COVID-19 Work Safe Plan conditions, albeit with the industry-wide problem of lack of parts.
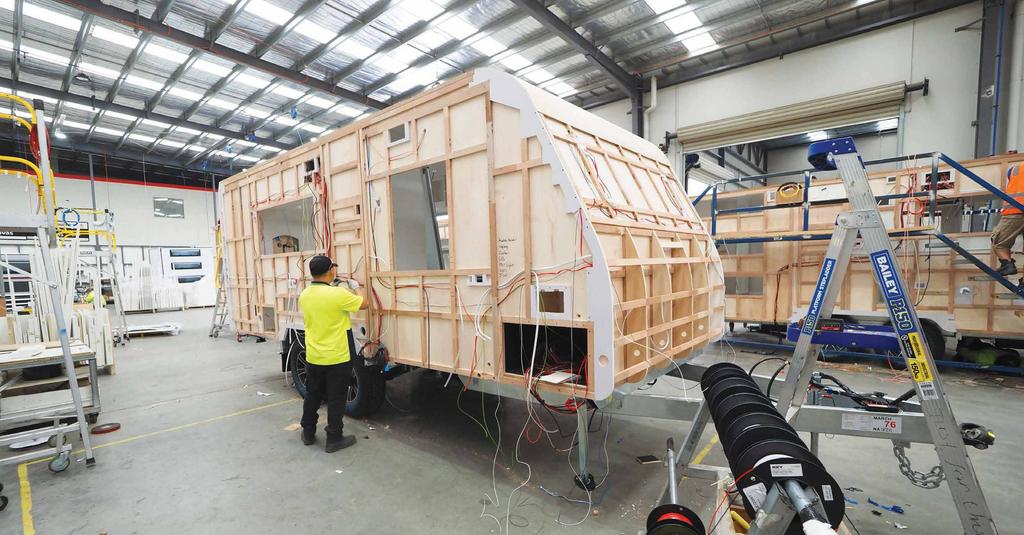
Rogy Matthew Karottu, Product Program Manager, hard at work
New Age has grown into one of our largest caravan manufacturers with an annual output of around 2000 vans and campers. To keep up with production, the company employs five full-time engineers to finalise each van's specifications and component list. Product Program Manager, Ro›y Mathew Karottu, showed me the computerised 3D modelling and examples of digital testing that goes into each van. He explained how a new model undergoes digital Finite Element Analysis before going through six months of real-world testing, including a 20,000km simulated run on the company test rig and hard driving at the Anglesea test track.
Manufacturing manager David Lawrence took me through the initial stages of the build and explained that each van was tracked through the build on a computer program to keep up with parts needed to complete the van. He told me production schedules were out to 12 months and that output was running at 12 vans a day across 12 different models and 178 variations. Even at reduced levels, the business employs over 280 workers.
The build starts with fitting suspension, wheels, water tanks, and other components to the hot-dip galvanised chassis from Hilton Manufacturing in Dandenong. The three-piece plywood floor gets its vinyl covering and then moves along the assembly line for the fitting of walls and roof. Next, frames are formed on a jig from Meranti and then bolted to the chassis.
With the walls in place, licensed workers oversee the wiring and plumbing while insulation is fitted between the timber studs before the cladding is applied.
The furniture is all built in-house from lightweight Italian ply. To speed production and guarantee consistent quality, the company has recently made a $1m investment in a new Rover edge bander and CNC table that cuts the ply sheets perfectly every time and completes the furniture with a neat radius edge.
Before the current industry supply challenges, the average build time for a van was 10-14 days on the very organised and efficient production line. The current supply situation has seen these build times increase with also longer-than-usual order lead times. On completion, vans go through a quality control section before a thorough water test. Each van is weighed on certified scales, and the compliance plate is fitted for delivery.
New Age has a dedicated warranty team, and they also have one of the best warranty policies in the industry. They are one of very few manufacturers we have seen that complies fully with Australian consumer law. In addition to their three-year warranty, they have a free one-year roadside assistance package for events like flat tyres and emergency towing.
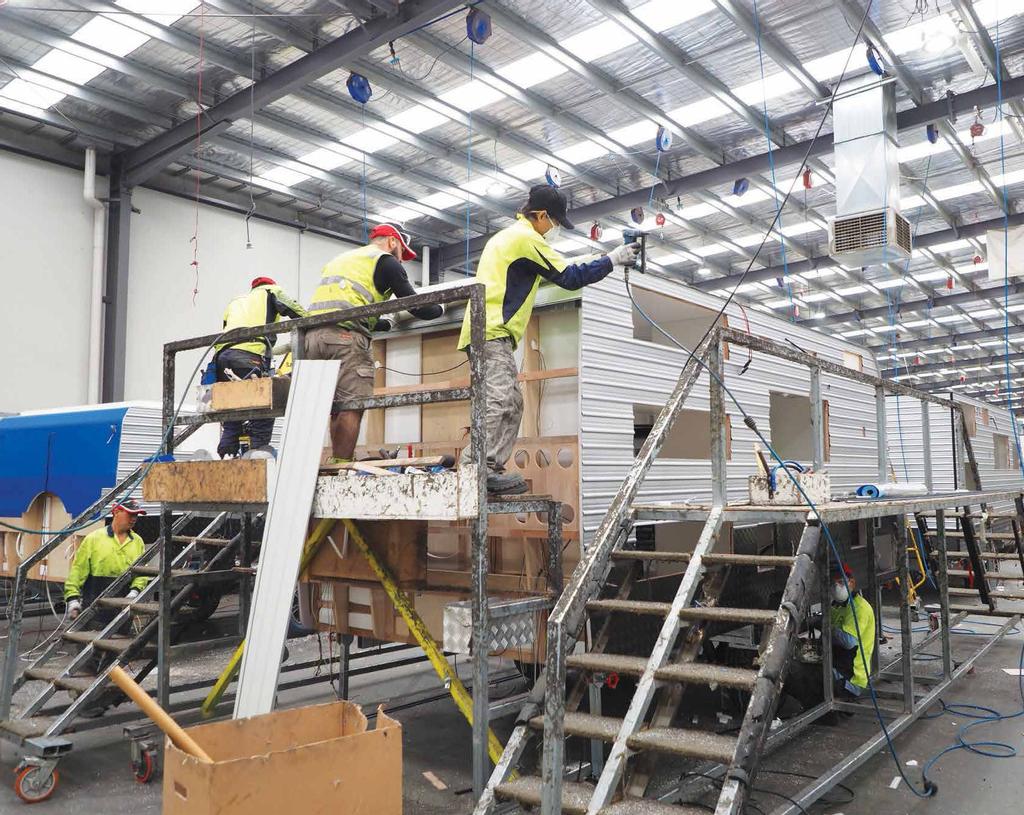
Installing the wiring is a delicate job