Behind the scenes at BMPRO
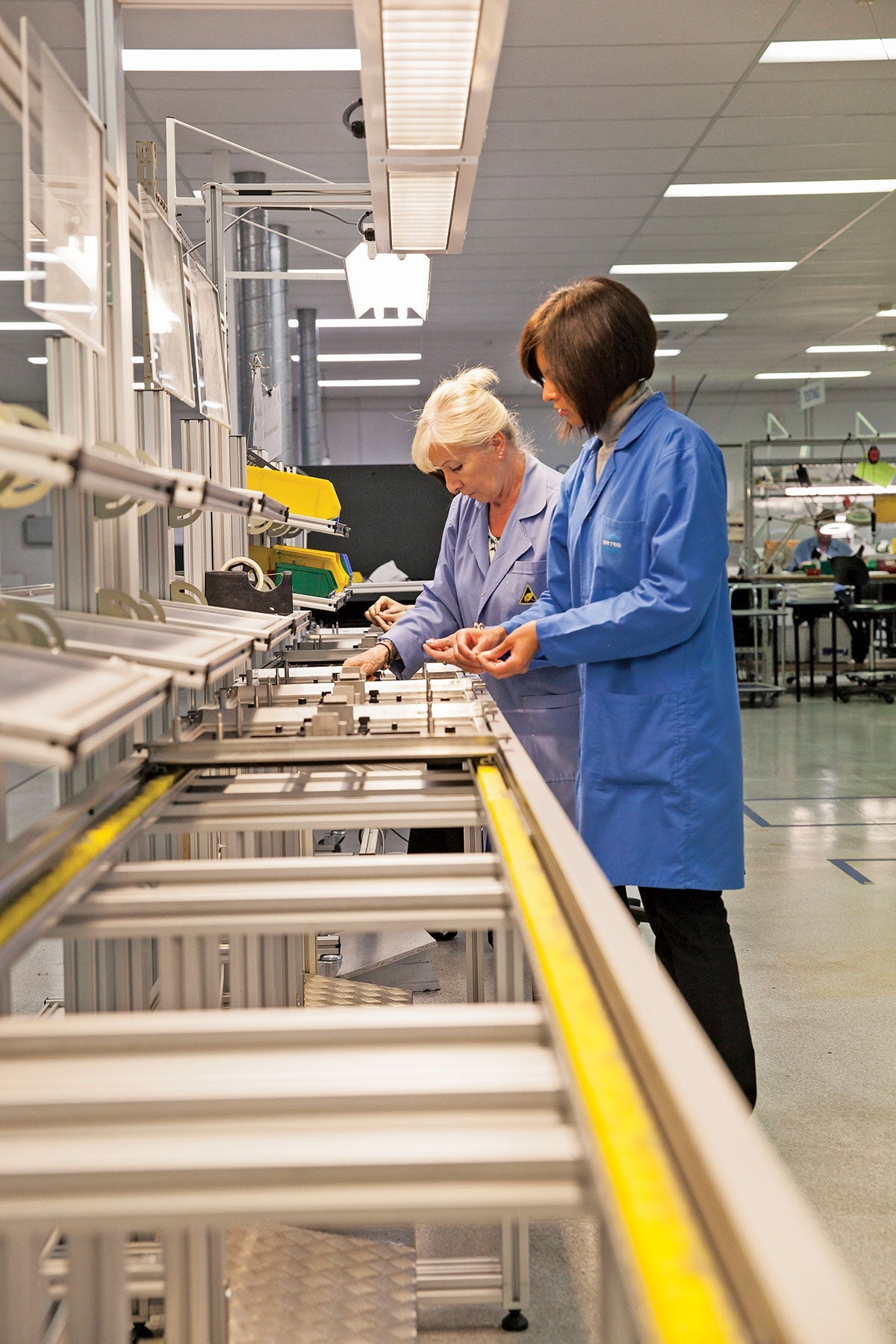
Join us as we tour through BMRPO’s factory in Knoxfield, Vic, with managing director Louise Bayliss and learn more about this Australian company dedicated to ensuring Aussies have reliable and innovative power management solutions for their RVs.
With more Australians hitting the road with a caravan or hybrid in tow, there has been a rising trend of adventurers wanting the capability to head off-grid for either short or extended periods of time, and potentially without the backup of gas. And with that comes a requirement for adequate and high-quality power management solutions that can withstand Australia’s tough conditions.
BMPRO is one of Australia’s leading power management solution manufacturers, and with its parent company, Setec BMPRO, BMPRO has been designing and producing power-related products for more than 55 years.
The large Setec BMPRO facility is based in the Melbourne suburb of Knoxfield and encompasses everything from the customer service team through to the research and development department and manufacturing line. Louise Bayliss, the managing director of Setec BMPRO, was happy to lead a tour through the facility and share some insights on the company and its many products.
History of BMPRO
Setec BMPRO was founded in 1968 (originally known as Scientific Electronics and then Setec) and was focused on designing AC to DC power from the very beginning. In the early 2000s, Setec expanded into the RV industry, working alongside Jayco, and it was in the years that followed that the BMPRO brand and range of products were developed.
As the daughter of Setec BMPRO’s founders, Peter and Jill Lloyd, Louise has been at the helm of Setec as managing director since 2004 and has overseen the creation and expansion of the BMPRO range that we’ve come to know and trust.
Setec BMPRO’s experience working in the industrial fields ensured the company was in a good position to move into the caravanning space, Louise explained as we began the tour. “Our acquired expertise has strategically positioned us through the establishment of rigorous quality controls, adherence to ISO standards, and compliance with other international business and design standards. This enables us to seamlessly apply our knowledge and controls to ensure the production of high-quality and reliable electronics for caravans.”
And in the years since, BMPRO has been very successful in the RV market, and its products can be found in a wide range of caravans, motorhomes and RV models around Australia and North America.
Where the magic happens
All BMPRO products are designed, built and tested at the Knoxfield facility, overseen by trained staff and automated machines to ensure every product is up to BMPRO’s high quality standards. Guiding the entire process, the product manager orchestrates the initial stages of design. Working closely with customers, conducting market research, and overseeing testing to determine product feasibility — all of these activities unfold within the large research and development department, marking the crucial nexus where ideas are transformed into tangible designs.
“Throughout the challenges posed by COVID, securing electronic components became a hurdle, as it did for many manufacturers. Consequently, we found ourselves engaged in extensive redesigning of existing products during that period," Louise explained. "However, it's important to note that the primary thrust of the R&D department remains on the creation of novel products or the enhancement of existing ones. Much of our work is inherently creative and innovative, spanning tasks from strategically placing components and circuits on the board to utilising software for programming the products in focus.”
Inside the R&D department, the system testing group shoulders the responsibility of ensuring seamless integration of all products within a system, while also ensuring compatibility with other devices and appliances within the caravan. The testing environment of the systems testing group is surrounded by air conditioners, solar panels, batteries, and fridges — all sourced directly from caravans. This immersive testing setup ensures a comprehensive evaluation of the products in real-world scenarios within the caravan ecosystem.
The factory tour
While the R&D department serves as the creative hub where products are designed, the factory functions as the powerhouse that breathes life into these designs. Designed for efficient and effective flow, the factory production line starts with the raw materials warehouse, moving to the picking lines, circuit board creation and loading, multiple stages of testing and then the final outward good warehouse.
BMPRO is a proudly Australian company — “95 per cent of our products are designed and made in Australia, which is quite a point of difference to many of our competitors in the space, so we’re pretty proud of that,” Louise commented.
Raw materials — such as printed circuit boards, enclosures and components — are brought in from overseas, but all of these have been made to BMPRO’s drawings and specifications. The drawings and qualifications are completed by BMPRO’s Australian-based engineering team, while the quality engineer based in Asia does further testing and there’s a quality assurance (QA) stage for the incoming materials.
“Our unique approach involves executing all manufacturing stages within the factory, a distinction not universally adopted by competitors. This comprehensive in-house process enhances our capacity to swiftly produce and dispatch products, contingent on the availability of raw materials. Beyond expediting production, this approach has notable quality benefits. Our engineers have direct access to the production line, enabling them to promptly address any issues and exercise complete control over the entire manufacturing process,” Louise said.
Once the materials are picked into job lots, the production line follows the U-shape of the factory, with a variety of stations comprised of either automated machines or skilled staff. Several of the stations were empty during the tour, and Louise explained that this was because BMPRO is “a low-volume, by world standards, high-mix facility. All staff are cross-trained, so they’ll move around to different stations depending on what products we’re running. In a run we normally do around 300 units, so it only takes approximately a day and a half to complete.”
The manufacturing process at BMPRO involves a series of automated machines and meticulous manual steps to ensure product quality. Automated machines load blank BMPRO-designed circuit boards with components, solder, and conduct inspections, alerting operators to any errors.
For high power-related products, larger components like capacitors are manually inserted, and boards pass through a wave-solder machine. Some products receive additional protection from humidity and water through a conformal coater.
After assembly, boards undergo rigorous testing, including using a bed of nails tester for specific electrical contacts. The final stages involve building the board into a mechanical enclosure, performing additional testing, and scanning to meet BMPRO's quality standards.
Emphasising a focus on quality throughout the entire process, BMPRO's approach includes a just-in-time manufacturing philosophy, keeping a small finished goods section for flexibility in production based on orders and available materials.
Industry insights with BMPRO
What are some of the ways BMPRO has been changing or growing as a company recently?
“We're focusing on two key areas. First, we're elevating the business to the next level, experiencing significant growth in both the Australian and US markets through new products and services. This includes substantial investments in personnel to establish structures, processes, and controls for sustained growth.
“All products for the North American market are designed and manufactured in Australia, showcasing our ability to compete with quality products and contribute to Australian capability through exports.
“Secondly, we are committed to ongoing investments in our product development and manufacturing capabilities. This involves integrating new machinery to ensure competitive pricing and embracing automation and advanced manufacturing for enhanced efficiency."
Have the new AS/NZS 3001.2:2022 electrical standards impacted the production of batteries, particularly when it comes to the requirements as to where batteries are stored?
“The standards and requirements as to where the batteries are located haven’t impacted production of our batteries. Our Invicta range of batteries have had the full certification standard for many years and are fully compliant to the new standards as the battery has had full compliance to the IEC62619 standard.
“Unfortunately, much of the information circulating is inaccurate or misinterprets the standard. As power management experts we aim to offer an objective interpretation of the standard especially around the Lithium batteries, emphasising its role in safeguarding lives and property through stringent safety measures. BMPRO is committed to compliance and certification, providing proof of rigorous testing to assure manufacturers, recreational vehicle users, and insurers that our batteries adhere to the standard’s safety goals, rather than attempting to manipulate it.
“The key point for the safety of lithium batteries is the statement ‘All lithium-Ion batteries shall comply with IEC62619’. A ‘battery’ includes both the battery management safety system and cells. Having only certified cells does not take into account intercell propagation and how the BMS (the key safety component) performs under adverse conditions to prevent any critical failure such as thermal runaway. Only when the battery is IEC62619 certified can you be sure that all aspects of the battery, including the BMS and cells, are fully safety tested and compliant.
"A cell is a single encased electrochemical unit, while a battery means two or more cells which are electrically connected together and fitted with devices necessary for use, such as a case, terminals, marking and protective devices. A single cell battery is considered a ‘cell’, regardless of whether the unit is termed a ‘battery’ or a ‘single cell battery’ (ref. UN38.3)
“BMPRO have put together a document about how our batteries are made to the new standards that came into effect at the end of November 2023,” Louise said.
The document is available to read here.
If more batteries are being stored externally, what should caravanners check for to ensure the safety of their batteries?
“Most will be installed in a metal box for protection — but it’s important to check and make sure the battery is in an area that’s protected from anything that could puncture it from below, and ideally is not completely exposed to the elements.”
The ingress protection (IP) rating of the battery is another important factor to consider. This rating denotes the resistance of the enclosure against dust or liquid intrusion. “It’s important to ensure you’ve got the right kind of battery if you’re planning on going offroad where water exposure may occur,” Louise advised.
“Most of our batteries have an IP65 rating which allows protection from water jets, so they’ll be protected from rain and similar amounts of exposure but can’t be submerged in water for long periods of time. BMPRO and our battery manufacturer agree that the IP65 gives enough protection for minor river crossings. Looking ahead, BMPRO is set to introduce a fully compliant battery with an IP67 rating. This enhanced rating ensures protection against more extended periods of submersion, making it suitable for those who require batteries for prolonged and frequent river crossings."
What would you consider some of your most popular products for the RV community?
“Our BatteryPlus35, which is our power management system, is seamlessly teamed with our Odyssey system — a caravan management system with a touchscreen display.
“The Odyssey connects to the BatteryPlus35 and has a screen and a phone app so you can keep track of your power consumption, power sources, battery status, lights and tanks. It will also control the slide-out if you’ve got one installed. We have a range of smart sensors, including tyre pressure monitoring system (TPMS) to it and gas bottle sensor, which will send information back to the Odyssey app.
“The BatteryPlus35 and the Odyssey is our main product that the caravan manufacturer installs. It can’t really be installed aftermarket though. If people want to make their RV a little bit smarter, we do have the ProSmart range, which is a Bluetooth monitoring system that allows you to have up to 40 Bluetooth sensors connected, as well as up to four water tanks.
“If you do have the BatteryPlus35 and Odyssey installed, there are a lot of things owners can add to their system after purchasing the RV, a shunt for the inverter and a DC-DC boost charger, such as our MiniBoost. The DC-DC charger is particularly important as it offers smart, quick and safe charging. We’ve got a wide range of products that cater to both RV manufacturers and the public who want to expand their van’s power setup.
“You’ll normally need to go to an auto electrician or dealer to install products such as in inverter, which are purchased through a retail store or dealer. Some people can [do it themselves] but they need some knowledge.”
Does BMPRO have any new products on the horizon?
"We have several products scheduled for release in 2024, including a BMPRO inverter range fully compliant with the latest electrical standards and tested within our systems. Additionally, we are developing a 60A charger and a high-powered system with capabilities of up to 100A, addressing the demand for faster charging in large lithium battery setups.
“Our upcoming expanded Invicta Lithium battery range will feature a Bluetooth battery app, ensuring full compliance with the new electrical standards.
What advice would you give caravanners looking to expand their power setup?
For caravanners looking to enhance their power setup or for those with electric vans, it's crucial to understand their usage patterns — consider whether they predominantly stay at caravan parks, go offroad occasionally or frequently. Tailoring the battery management system to their needs is essential. For those using caravan parks and mains power, a standard 35A system is usually sufficient.
“Offroad enthusiasts will benefit from a DC-DC charger and should assess additional solar needs, especially if operating gasless or powering 240V appliances through an inverter.
“For caravanners well-versed in power systems seeking information on off-grid setups, our website provides comprehensive resources. BMPRO's expertise includes extensive testing on the differences between lithium and AGM batteries, aiding users in selecting the system that best suits their requirements.
“One key factor discussed is the depth of discharge. AGM batteries can only discharge to 50 per cent, while lithium batteries can go up to 80 per cent. Lithium batteries offer longevity, lasting for 6500 charges and discharges compared to AGM's 650 cycles. However, the higher upfront cost of lithium batteries, approximately four times that of AGM, is an important consideration.
“In the event of product issues, customers can contact their dealer, who will then reach out to us. Alternatively, our website provides a customer service phone number and email address, along with a warranty and repair form. We conduct thorough checks to ensure the problem is with the device and not due to installation or user error. If the product is within warranty, we offer a replacement. Out-of-warranty products can be sent for repair through our service centre."
For more information
BMPRO has an extensive amount of information on its website for those interested in the company’s many power solutions or want to understand lithium batteries and the new electrical standards.
Contact details:
BMPRO
P: 03 9763 0962
E: customerservice@teambmpro.com
THE NEXT STEP
Are you ready to experience the freedom of the open road? Don't wait - Find your dream getaway now!
RELATED ARTICLES:
Australia's ultimate power and battery management solutions: BMPRO