Jayco Interior Fit Out: 2014 Tour
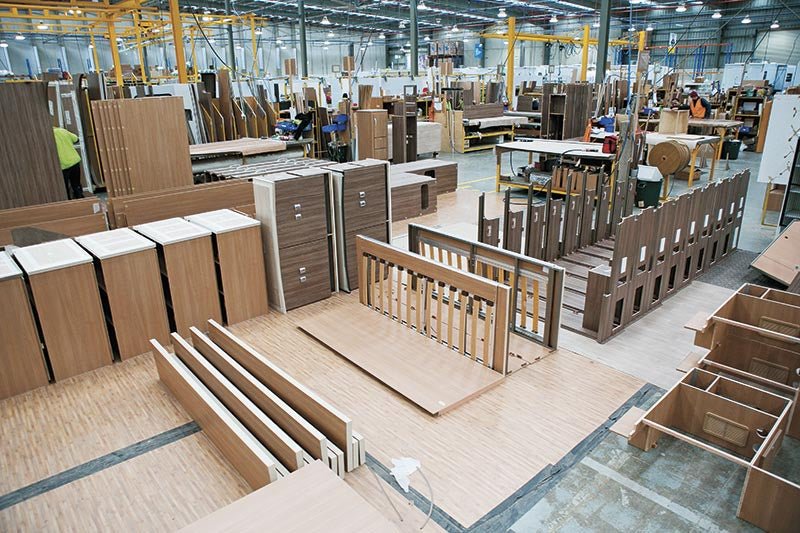
Jayco Australia founder Gerry Ryan’s long-standing affinity for European style has, unsurprisingly, found an excellent outlet in the interior design of all his RVs.
Jayco’s current interior style is a modern take on the traditional ‘timber-look’ interior so favoured by many Australian vanners. The Jayco Expanda’s cabinetry, named ‘Avakira’, is a light colour with a complementary vinyl floor, two-tone dinette fabric upholstery, pale benchtops and white walls and roof. It’s a classic combination that nicely blends modern European design with Australian practicality.
Jayco also offers lots of options for buyers to personalise their van and there are several alternatives for most of the internal finishes. Expanda customers have eight different cushion fabrics, or five optional leathers, to choose from when designing their van, as well as three Laminex benchtops, a second optional curtain fabric and another optional floor vinyl.
JOINERY
All Jayco cabinetry starts its life in the factory’s saw section. In order to keep weight down, all cabinetry and furniture is made of plywood or a ply/polystyrene sandwich. While solid timber furniture would send the weight of a caravan soaring, plywood, made from many thin layers of wood bonded together, is a strong, lightweight alternative. Weight-bearing furniture, such as dinettes, also get an aluminium frame for extra strength. The ply and sandwich blocks are bought from an Australian supplier that sources the materials from overseas.
The saw section is a huge space with more than 20 towering piles of different types of ply reaching halfway to the roof, and high-tech machinery constantly buzzing and cutting. Many of the machines are computer-aided, reducing the risk of mistakes and ensuring accuracy. But a small amount is also done by hand, such as edging and gluing a round table.
Some machines cut ply into smaller pieces, others cut shapes into them and some do the edging and lining of things such as shelves and benchtops. How many times have you stuck your hand into a caravan cupboard only to find the inside edge of the shelf hasn’t been sanded or lined? Not at Jayco!
Once the materials have been cut and edged, they’re delivered to the furniture assembly section on the production line..
FURNITURE ASSEMBLY
This area takes up a massive amount of space, right in the middle of the warehouse, and it’s a hive of activity. Jayco staff work on individual stations, each focusing on building one component. One person might be building fridge cabinets, while another assembles bathroom vanities and a third works on kitchen cupboards. A lot of plumbing is also done at this stage, rigging up the pipes to items such as bathroom and kitchen sinks and showers.
Furniture components that will house appliances, such as a fridge unit or even a sink, have the appliance pre-loaded into it before it goes onto the van. Once the components have been fully assembled, they’re dispatched to the production line to be installed. And, as caravans are built from the inside out, this happens fairly early on the line, before the walls are erected.
As a van moves down the line onto the furniture-fitting stations, every item of furniture and cabinetry that needs to go into that particular van will be waiting there, ready to be loaded. Small or light components, such as bedside cabinets or even empty dinette modules, are simply lifted onto the van’s floor, while larger or heavier components, such as fridge units, require trolleys and several people to lift them.
The furniture is loaded across several stages of the production line, and it’s all screwed down after the walls go up.
SOFT FURNISHINGS
The soft furnishings are an important part of a caravan’s internal fitment and, unsurprisingly, Jayco’s are all made on-site. The department keeps in excess of 50 fabrics – all Jayco’s current lines, as well as old stock in case they need to fill an order for a repair of an older model.
About 47 people work across the cutting, sewing and filling department, producing all the soft furnishings for about 50 Jaycos a day, including 17 pop-tops, nine caravans, eight Starcrafts, 12 camper trailers, two motorhomes and one leisure home.
All interior fabrics and the Expanda tent materials are cut on the cutting floor by a Lectra machine, which is capable of cutting up to 30 layers of fabric at one time.
Once the fabric is cut, it’s moved upstairs in an elevator to the sewing section where the cushion covers, tents, pelmets, curtains and more are sewn into shape and have things such as zips added.
Downstairs in the filling room, the covers are stuffed to make cushions. Jayco furnishings are stuffed with high quality, antibacterial Dunlop foam in varying densities and grades. The foam is treated with antimicrobial protection to prevent mould, mildew and fungi, as well as anti-allergenic dust and mite protection. The cushions are filled by a low-tech, but very clever, vacuum. A piece of foam, cut to shape, is laid across a table full of holes with a vacuum below.
A piece of Dacron, for added comfort, is then placed over the foam, which is then covered with a plastic sheet. With the plastic in place, the vacuum packs the foam down to a manageable size, allowing the worker to easily stuff the cushion. The plastic is then removed and the foam returns to its normal size, filling the cushion cover. Genius!
Back on the production line, the soft furnishings are virtually the last part to be added to the caravan. The Expanda’s tents are installed into its moulded fibreglass front and rear just before the end and, at the very last stage, the soft furnishings are put in, right before the van undergoes its final quality check. Up to this point, the van’s interior looks quite shell-like but once the cushions and curtains are put in place, it really starts to look like a home away from home.
The full article appeared in Caravan World #531, November 2014. Subscribe today for the latest caravan reviews and news every month!