Cruisemaster XT, ATX Airbag and DO35 review
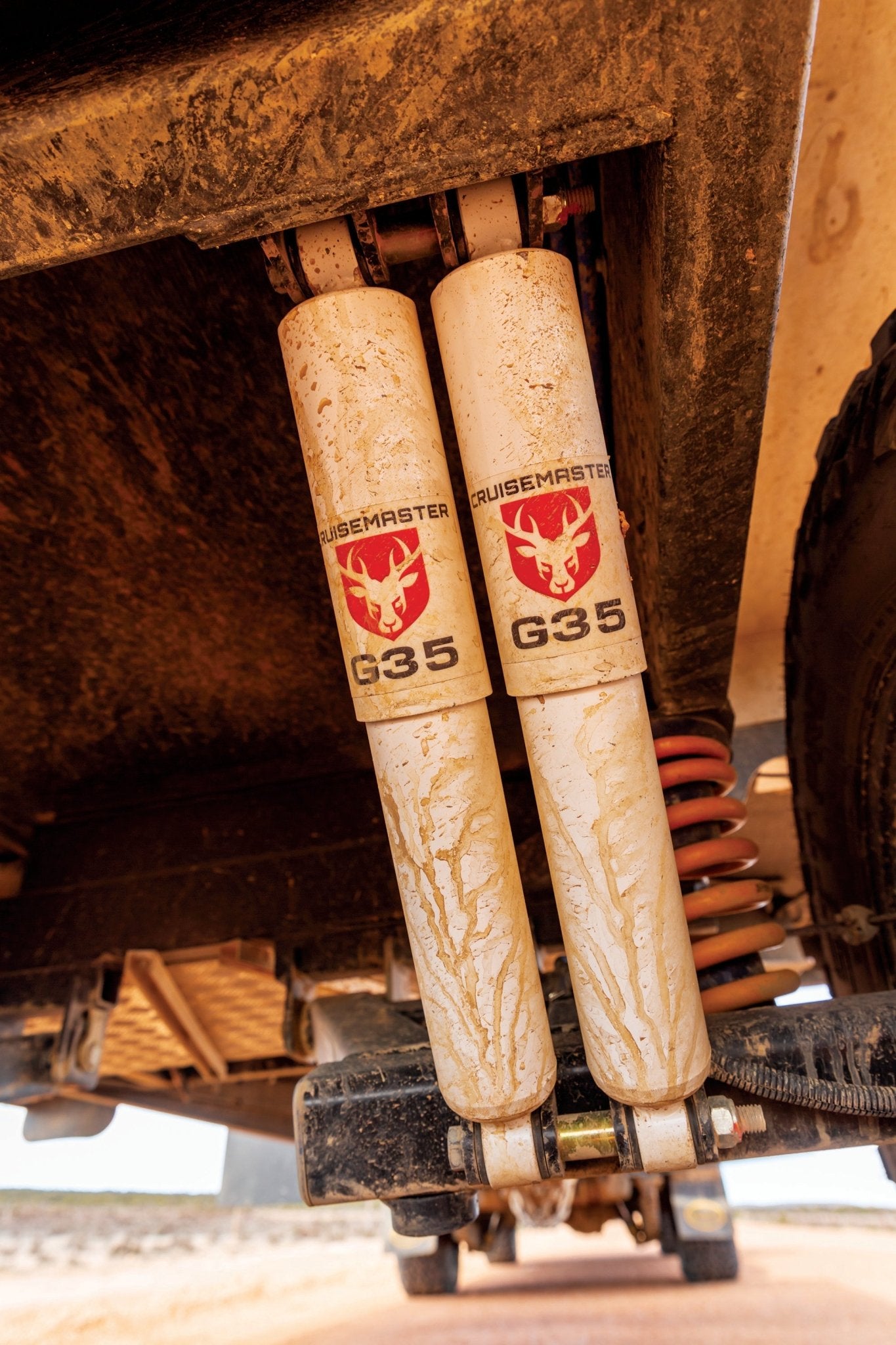
RV innovators, Zone RV demand the best of suppliers to match its own exacting standards so suspension and coupling duties on both of our Z10.0 Expedition Series campers which we took on an epic adventure to the Great Australian Bight in 2018, were handed to Cruisemaster.
Cruisemaster has been supplying top-end caravan and camper manufacturers with a range of independent suspensions and hitches for more than 40 years and in that time has forged a reputation for durability and ease of use in its four suspension options and famous DO35 hitch.
We had a set of XT and ATX (with optional airbags) independent trailing-arm suspensions fitted to the Z10.0s for our trip to the Bight, as well as the latest iteration of the DO35 hitch.
With more than 9000km covered, including days on the challenging limestone escarpment that defines the Bight, we had a real test on our hands.
IN THE FAMILY
Three generations of engineering skill and countless kilometres of real-world testing have earned Cruisemaster its place as a world leader with its steely tough suspensions. Cruisemaster claims to be the best and are so confident of its position in the market it backs up its products with a conditional five-year warranty.
Known initially as Vehicle Components, which built a range of trailer components, the company changed the name in 2018 to the more widely known Cruisemaster — the brand of its popular suspension systems.
Founder, Arthur Goddard designed and built his first trailer parts 41 years ago from a factory in Albion in suburban Brisbane. The original production included leaf spring suspensions for specialised machinery and machining axles and hubs on a lathe. Early innovations included an automatic ratchet handbrake for trailers and heavy-duty jacks and jockey wheels.
When Arthur’s son Chris joined the business in 1998, he brought experience from his automotive manufacturing background to modernise production and turn the company into an industry innovator. He went on to introduce its first Independent AT system on leaf springs and then XT Air, before designing the first XT coil version, which was launched on a Boroma caravan in 2009.
Contrasting against the humble beginning is its large factory complex in Brisbane’s north with three robot welding booths, specialised CNC machines, automated lathes, spray booth and a fleet of remote area testing vehicles that have traversed nearly every inch of our most isolated tracks trying to find the limits of the durability of new products. As Technical Operations Director and grandson of the company founder, Andrew Goddard told me they try to break components, so their customers don't. As well as investing in sophisticated manufacturing equipment, Cruisemaster relies on hard-hitting computer programmes to facilitate its designs.
DESIGNED TOUGH
Before production, all components are planned in a digital 3D space and put through digital Static and Dynamic Finite Element Analysis. This sounds impressive, and it saves valuable time in the development process by checking on the interaction between parts and establishing durability in a virtual reality space. Further testing is carried out on an in-house dynamic test rig that simulates thousands of kilometres of real-time testing of prototypes before going through even more testing at benchmarked test tracks such as Victoria’s Anglesea Proving Grounds and remote tracks around Australia.
They offer four independent coil sprung (and two airbag sprung), trailing-arm suspensions, ranging from simple but innovative on-road systems to extreme-condition products that are the toughest available.
Coils have advantages over leaf sprung suspensions by having lighter un-sprung weight and being more efficient at dampening road vibration and shock. In extreme cases, you can usually limp home on a broken coil, whereas a broken leaf spring will likely leave you stranded.
Cruisemaster trailing-arm suspensions have an A-frame connected to the chassis leading to an axle at the base, to which the wheel is attached. The leading end of the A-frame is fixed on a pivot in two places on the chassis to avoid twist and ensure vertical wheel travel. Coil springs between the A-frame and the chassis soften the movement as the van moves across uneven ground and shock absorbers dampen the progress of the spring.
Because each arm is independent of the other, there is no transfer of shock or movement as would be seen in a beam axle setup. And because the arms can be constructed to virtually any length, there can be much longer wheel travel in the trailing arm system.
The base model, Cruisemaster GT, is targeted at on-road vans and uses cast arms, King coil springs and single shock absorbers with each side offering a smoother ride in comparison to leaf-sprung arrangements.
Next up in the range is the recently released CRS2 — Country Road Suspension — with beefier fabricated arms and heavier rated springs and dampers than the GT. It’s designed for long runs on our worst blacktop and dirt roads but, with 30mm dampers, it isn’t recommended for endless corrugations like those found in Cape York.
The 2600kg XT Coil and 2800kg ATX airbag suspension under the Zone RV 10.0s on our Great Australian Bight adventure are in the high end of the Cruisemaster catalogue, and both systems survived some incredible punishment during our long 9000km journey.
XT SUSPENSION
Current XT systems are a fifth-generation design and are built in-house using techniques unique to Cruisemaster. Components are laser tube cut and robot welded on Pulse MIG rigs to precise tolerances. 50mm stub axles are then hand welded with a technique developed over the years to ensure there is no warping from the heat during assembly. Years of experience building over 80,000 independent suspensions have helped Cruisemaster design machinery and jigs that provide correct wheel toe-in and camber every time, meaning the trailer wheels run true in lateral and vertical planes.
Australian BHP steel is used in the all-important A-frame and in the Gold Coast-manufactured King Springs. Brake drums are also Australian-made in Adelaide, while Japanese bearings are built to Cruisemaster specifications.
The use of 130mm travel twin shocks means there is twice the oil to spread the load and helps disperse heat quickly over rough terrain. Either 35mm or 40mm shock absorbers are available in XT, depending on load requirements. The 35mm variants on the Zone 10.0 worked just as well at the end of the journey as they did out of the factory.
ATX SUSPENSION
Offroad caravans and campers have grown in complexity and weight over the last decade, as owners demand the best of everything and the ability to drag their rigs into remote locations. Cruisemaster recognised the trend and introduced the most robust and most sophisticated suspension it could engineer. According to their marketing, the ATX (All Terrain eXtreme) system is the “biggest and baddest”, and it is probably right.
Based on a beefed-up single arm platform, it comes with upgraded racing style, remote reservoir, monotube shock absorbers, 63mm stub axle and larger bearings and a choice of upgraded King Coils or rolling sleeve Firestone airbags as on our Zone test camper. Wheel travel is increased to 144mm over the 130mm of the XT, and because the airbags can be adjusted, their load can be varied between 2200kg and 2800kg.
Adding to the appeal of the airbags is the ability to level the van when camping by adjusting the height of each side individually and having an onboard air tank and compressor to adjust tyre pressures, which we used continuously through our trip.
DO35 HITCH
This is version three of the drop-on 3.5t coupling and it’s claimed to be the strongest yet. A forged steel yoke with a universal joint pivoting 360 degrees for sideways movement connects to a bearing for fore and aft movement to provide a trailer connection with extreme articulation. A polyurethane bumper absorbs shock and the drop-on locking mechanism locks onto a tapered tow pin when lowered.
The loud metallic ring when the pin locks makes for a foolproof connection, further reinforced when the dust and debris proof covering cap is fitted.
If the cap doesn't fit, you haven't locked the system properly.
We checked both hitches near the end of our trip, after having had both buried in sand and dipped in water to find both were like new underneath, an outstanding result for what was one of the most challenging trips we’ve undertaken.