Attention to Detail
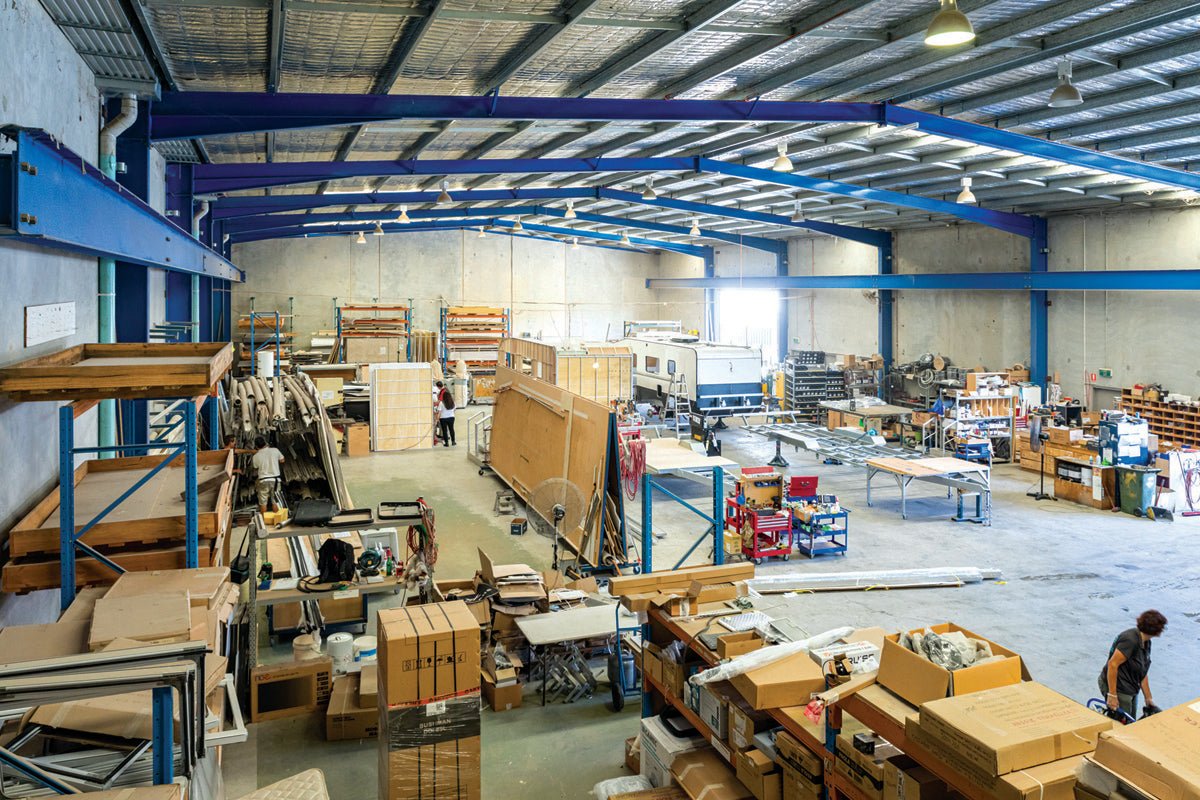
Factory tours have always fascinated me, which is probably why I love watching MegaFactories on the telly. I'm not 100 per cent sure where this fascination comes from, but I have a pretty good idea.
I suspect it stems from my childhood when, while I was on school holidays, my Dad would take me to his work in one of the world's largest bulk sugar terminals. These visits would inevitably end up with me following Dad around on his daily business while he explained all the processes behind bulk sugar handling, from when it comes from the mill, all the way to being loaded onto massive bulk carriers.
It was all very fascinating as a child and I suppose that process of seeing a raw material enter a shed at one end, and leave at the other as a finished product has never left me.
That's why I always like it best when I head out on a caravan review and it starts at the factory where the vans are built. I'm rather spoilt here in South-east Queensland too, with several high-end manufacturers calling this part of the state home. I've had the pleasure of touring through the ZONE RV, Bushtracker, Rhino Max, Paradise Motorhomes, Sunland and Winjana RV factories. But on this occasion, I was the guest of the Spinifex Caravans factory at Deception Bay, north of Brisbane.
Spinifex has occupied this factory for nine years now and has been in operation for 13. A successful local business, Spinifex currently employs 23 workers on the floor and in the office.
Apart from building its own vans, Spinifex offers a repair and service bay (for any make or model of van) as well as being a preferred repairer for several insurance companies.
The owner of the business, Steve Thompson, is all about building the best possible van for his customers. He's also the kind of guy who goes out there and uses his products in the way they are meant to be used, often spending extended periods of time in the middle of nowhere testing his vans to the limit. It is this basic premise that is echoed throughout all the designs in the Spinifex range.
With a background in the caravan industry starting from the age of 15, Steve now boasts more than 26 years' experience. As a qualified motor body builder, he knows his way around all aspects of caravan manufacture.
Thompson also doesn't mind hitting the water, and elements of design and products from the marine world have, over time, found their way into Spinifex's caravan designs. Adapting products from alternative industries has never scared the team at Spinifex, and that is why they’re now forging ahead with bringing 48V electrical systems into their vans.
Teaming up with Safiery, from 2021 Spinifex Caravans will become an OE supplier of 48V systems and offer it as a standard fitment across its range of offroad caravans.
Mark Evans, who was my tour guide for the morning, is one of the sales and customer service experts and has been with Spinifex since 2017. Starting on the factory floor, he has a wealth of experience in the automotive industry, with the past 12 years dedicated to caravans.
He took me through the entire process from start to finish. We even had to take a short drive Caboolture to visit Spinifex Caravans' own off-site fabrication shop.
It is here that the chassis for every Spinifex van is built on a jig to ensure maximum accuracy, before being sent off to be hot-dip galvanised. Being able to see a chassis in its raw state gave an insight into the level of detail in a Spinifex build. Seeing the 'V' notches cut into the rails to allow for the galvanising to not only get inside the rails and cross members, but to also allow the excess to drain out was impressive.
Also manufactured at the fabrication shop are the aluminium toolboxes, generator boxes, wheel arches and the full-width stone guards.
Back at HQ, Evans started the tour of the factory, but perhaps it is what goes on before a piece of steel is even cut that is most important.
Each customer looking to purchase a Spinifex Caravan sits down with both a member of the sales team as well as David, the design manager. Where possible this is done face-to-face, but it can be done remotely if required.
With no two Spinifex vans being the same, this can sometimes be a lengthy process, but the final result for the end user is a van that will suit their needs perfectly.
From here, floorplans along with internal and external elevations are produced before final sign-off by the client. A chassis plan is also produced, and it is only then that the steel cut-off saw and MIG welder gets a call to action.
After the chassis has been galvanised, it makes its way onto the factory floor. As Spinifex is a bespoke manufacturer, there are only ever four builds on the go at any one time, at various stages of completion.
Starting from the floor up, the vinyl floor is laid before the walls are fitted.
The aluminium wall frames are all built by hand and are assembled on a jig for consistency and repeatability. The 30mm aluminium channels are pop riveted together while the corners are bolted to maximise strength.
The wall cavities are filled with 30mm styrene for insulation between the ply interior lining and the external fibreglass sheet. The roof is manufactured in exactly the same way.
However, the roof is the last piece of the puzzle and is fitted after all of the internal cabinetry has been installed and attached to the walls. This method makes for a solid unit that can withstand the constant rigours of offroad and outback touring.
Speaking of the cabinetry, it is all manufactured on-site in a designated area from lightweight timber and ply. Making sure that the whole process is kept in-house, hiding away on the mezzanine level and keeping an eye on everything on the factory floor is the upholstery shop. It is here that all of the lounge coverings and magazine pockets are made.
As well as manufacturing as much as it can on-site, Spinifex Caravans does whatever it can to source raw materials and products locally. If this can't be achieved, then the company will always look to use Australian-made products first, wherever possible.
After all the other processes have been completed, including the certification of all plumbing, gas and electrical work by an independent contractor, the van heads off to the weighbridge. Each van is issued with a certificate that is provided to the new owner at handover.
Overseeing the production line is Scotty, who joined Team Spinifex in 2018 and is the Production and Service manager. He has over 25 years of experience in the caravan industry and is a qualified motor body builder by trade. On the floor, the production crew have more than 70 years combined experience building and servicing caravans.
For those interested in acquiring a Spinifex van to park at their place, a bit of forward planning is required. Currently, the lead time is around four to six months, depending on the build, with each van taking between six and eight weeks to complete.